TIG question
Moderator: Club Officers
TIG question
A friend of a friend of a friend (etc) has a power supply/TIG torch setup for sale for fairly cheap, but it only outputs DC, so that means no Aluminum welding correct? I need some work done on an aluminum boat tower and we have a family friend who used to weld aluminum dog boxes and truck racks, but got out of the business...and sold all of his stuff...so he said he'll fix up my tower if I can find him a TIG machine. No AC output not the machine I'm looking for? It's cheap enough that I can buy the machine, buy the family friend beer while he welds for me, and still come out ahead of a quote I got from a shop for the work I want done...so I really want it to work.
-Ryan
-Ryan
Thanks for the response...unfortunately confirming what I thought.
As for the work needed, I've got a tower that was built for a different boat than the one I own, but it's close and it was cheap, so I bought it and have been trying to find an affordable way to get her right.. The shop I took it to said it would take them between 4 and 8 hours to do it because they would have to do one thing at a time...and then stick it back on the boat and decide their next move, take it back off and cut/weld, rinse and repeat. Our family friend didn't seem to think it's quite that hard...but who knows. Pretty much I've got a four legged tower that mounts to the deck of the boat, but the front two legs need to be about two inches further apart and the back legs need to be lengthened by about a foot (which if you followed the angle they're currently taking they'll end up too wide once you've lengthened them).
hopefully you'll see some pictures attached here that might help...
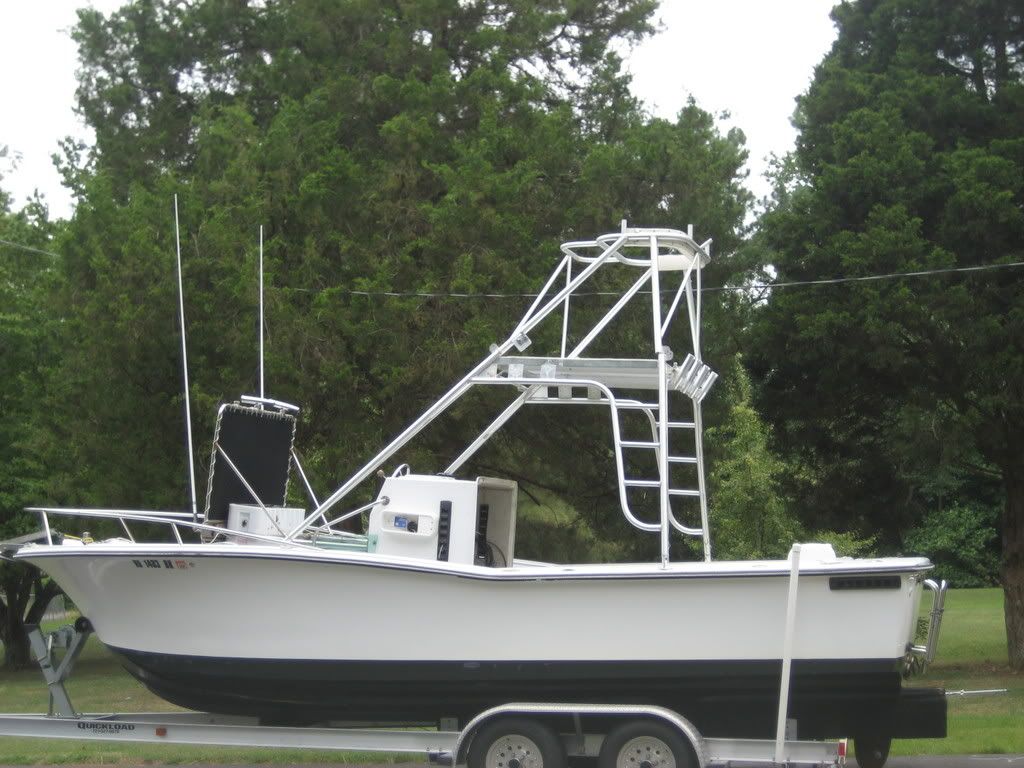
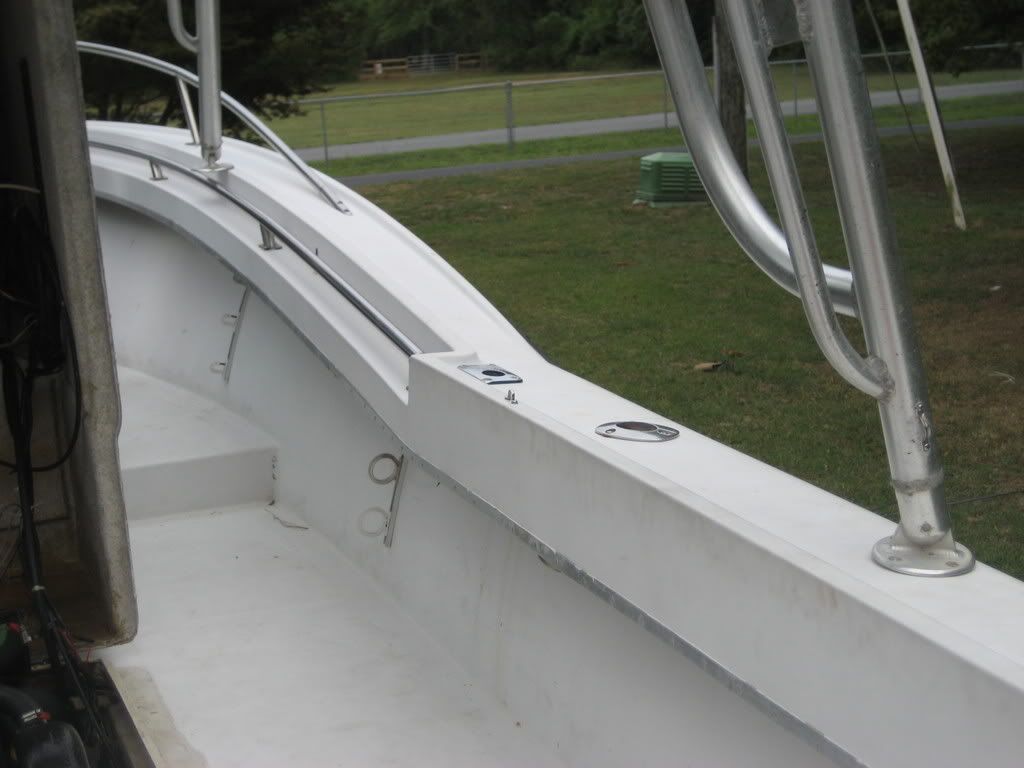
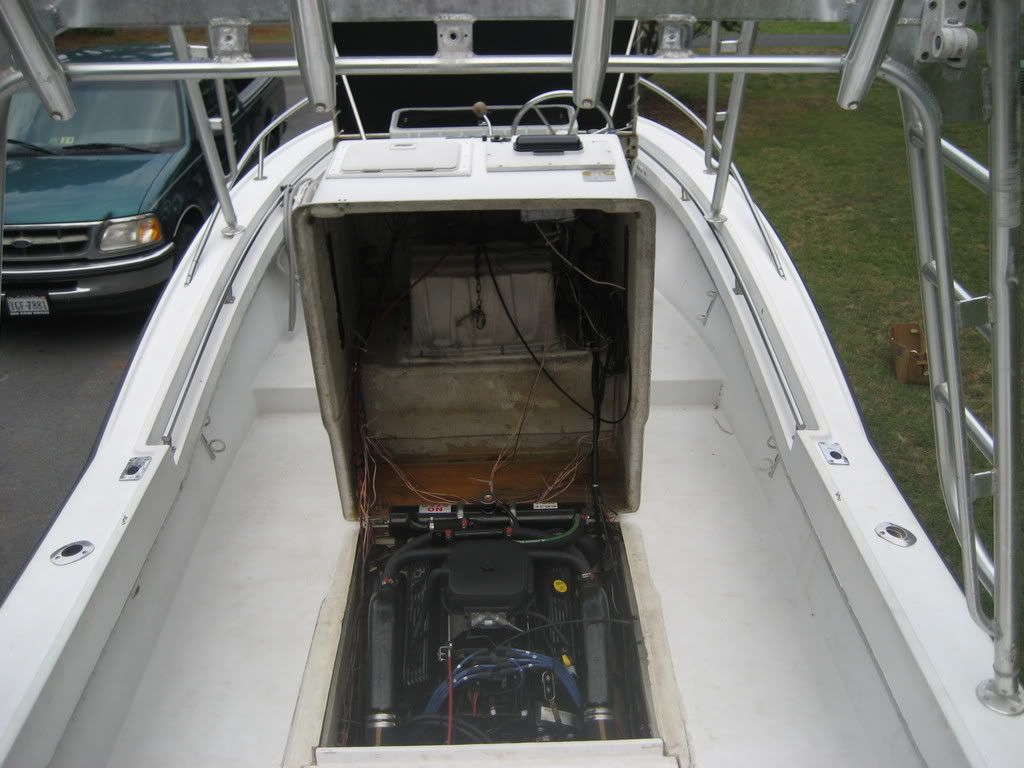
As for the work needed, I've got a tower that was built for a different boat than the one I own, but it's close and it was cheap, so I bought it and have been trying to find an affordable way to get her right.. The shop I took it to said it would take them between 4 and 8 hours to do it because they would have to do one thing at a time...and then stick it back on the boat and decide their next move, take it back off and cut/weld, rinse and repeat. Our family friend didn't seem to think it's quite that hard...but who knows. Pretty much I've got a four legged tower that mounts to the deck of the boat, but the front two legs need to be about two inches further apart and the back legs need to be lengthened by about a foot (which if you followed the angle they're currently taking they'll end up too wide once you've lengthened them).
hopefully you'll see some pictures attached here that might help...
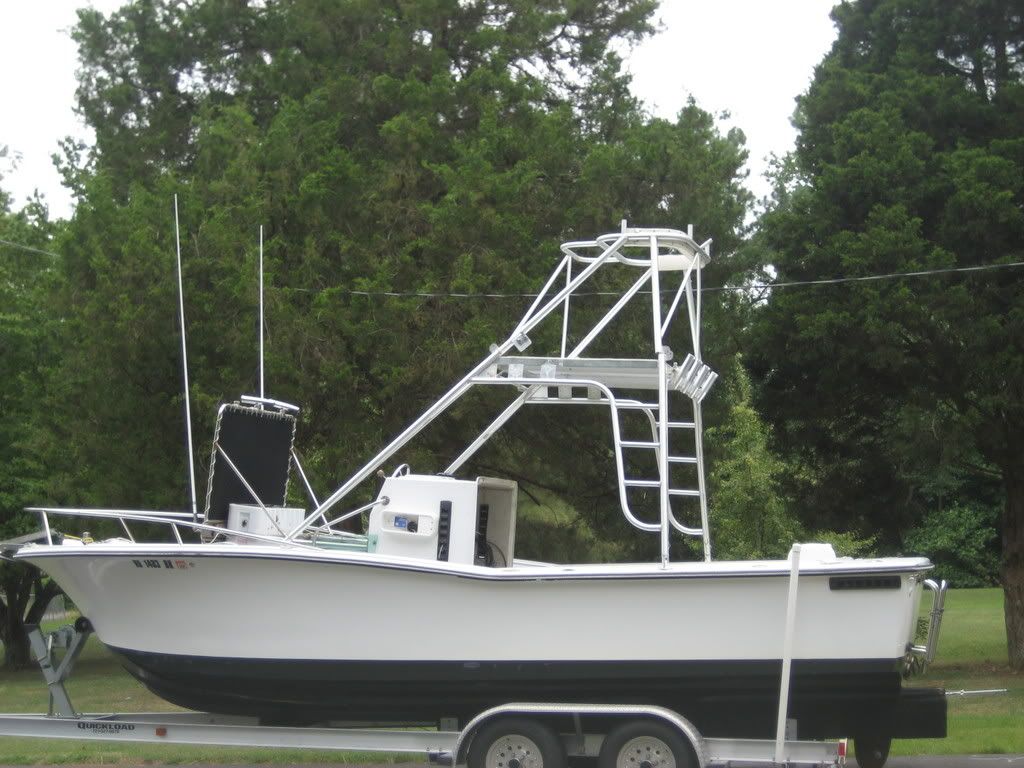
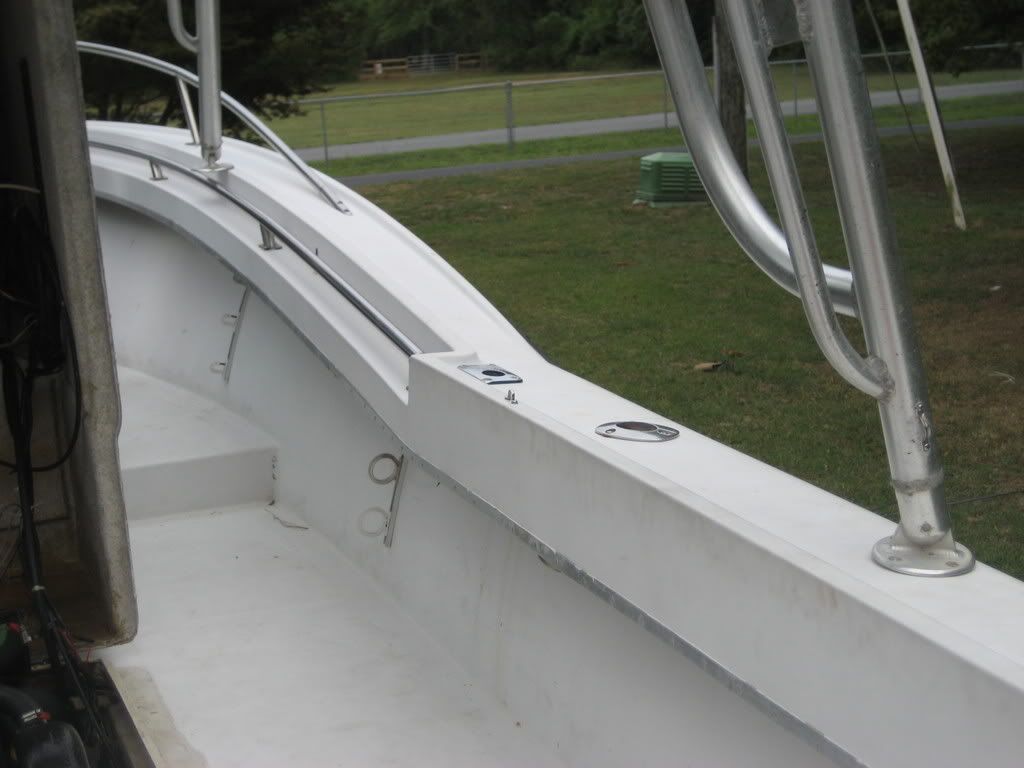
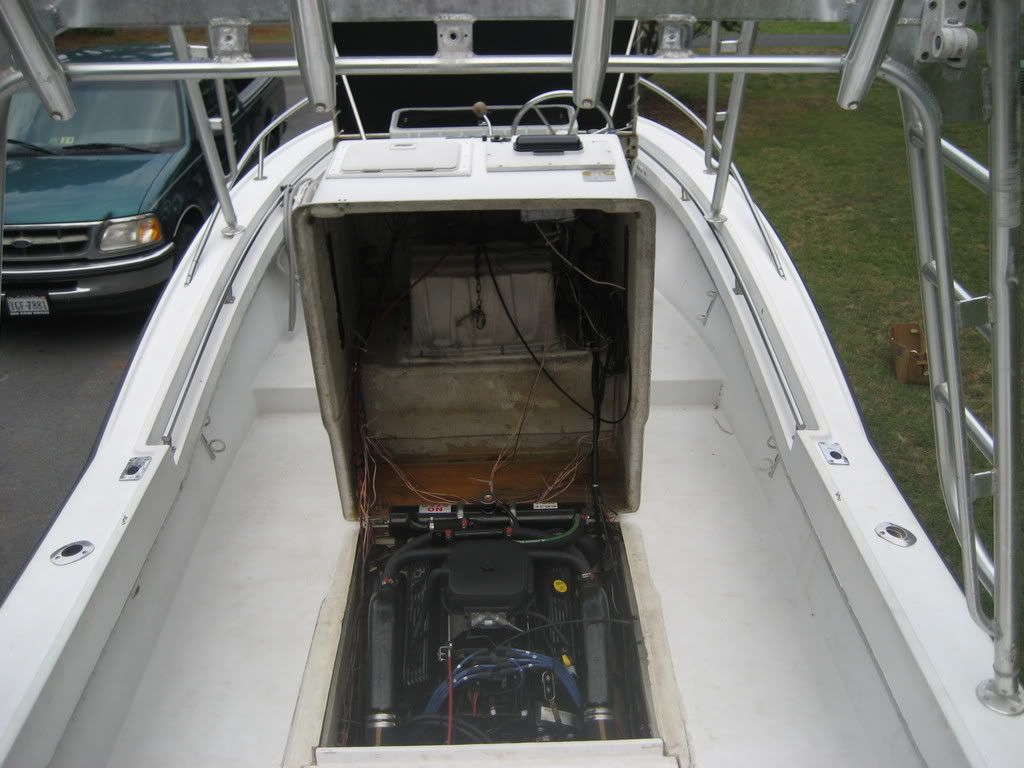
- Arya Ebrahimi
- Posts: 1896
- Joined: Tue Dec 14, 2004 10:58 pm
Thanks for the compliment and it ain't up here, it's 5 hours east of here...where boats like that belong (and people like me wish they were), but if you know of a shop around here that might can do it (or if you're looking for some work/money/beer Jonesy) I can trailer her up here.
In reality I'll probably need to just suck it up and bend over for the shop back home because while it sure ain't going to be the cheapest way to get the work done, it'll be the easiest, and really that's almost as good as cheapest...I was really just hoping that TIG machine I could buy would work for my buddy to weld it up back home one weekend cause that was going to be cheap and easy, but no such luck.
In reality I'll probably need to just suck it up and bend over for the shop back home because while it sure ain't going to be the cheapest way to get the work done, it'll be the easiest, and really that's almost as good as cheapest...I was really just hoping that TIG machine I could buy would work for my buddy to weld it up back home one weekend cause that was going to be cheap and easy, but no such luck.
Couldn't blame you. When I took it to the shop the guy walked out not knowing what I was bringing him and actually said "shiiiit, aluminum?" so I reckon that should tell me something...
I'm thinking of just biting the bullet and buying an ac/dc TIG machine because it's honestly within $200 of the quotes I was getting and to me spending the money and having a TIG machine AND a tower is well worth it.. That plan only works if that guy on Pirate (parker metal works) has machines that are worth a shit...that and I hit the lottery because I can't even afford to pay a shop much less the $200 extra dollars I'd pay if I just bought the dang machine...details, details...
I'm thinking of just biting the bullet and buying an ac/dc TIG machine because it's honestly within $200 of the quotes I was getting and to me spending the money and having a TIG machine AND a tower is well worth it.. That plan only works if that guy on Pirate (parker metal works) has machines that are worth a shit...that and I hit the lottery because I can't even afford to pay a shop much less the $200 extra dollars I'd pay if I just bought the dang machine...details, details...
You can weld aluminum using DC reverse polarity, but the weld quality lacks a helluva lot to be desired. i have some E4043 aluminum stick that i'm going to try out-of-position in the next few days, but at $26/lb, its expensive as hell.
-Henry
'98 XJ, '05 Grand Prix GTP, '86 Fiero, '70 M35A2, '77 M880
'98 XJ, '05 Grand Prix GTP, '86 Fiero, '70 M35A2, '77 M880
Yeah, and you can spooge on the part and keep you fingers crossed hoping it holds.hklvette wrote:You can weld aluminum using DC reverse polarity, but the weld quality lacks a helluva lot to be desired. i have some E4043 aluminum stick that i'm going to try out-of-position in the next few days, but at $26/lb, its expensive as hell.
Some info found with a quick google search: For example, to weld at 100 amperes it would take a tungsten 1/4" in diameter. This large electrode would naturally produce a wide pool resulting in the heat being widely spread over the joint area. Because most of the heat is now being generated at the electrode rather than the workpiece, the resulting penetration would probably prove to be insufficient. If DCEN were being used at 100 amperes, a tungsten electrode of
1/16" would be sufficient. This smaller electrode would also concentrate the heat into a smaller area resulting in satisfactory penetration.
The good penetration of electrode negative plus the cleaning action of electrode positive would seem to be the best combination for welding aluminum. To obtain the advantages of both polarities, alternating current can be used.
It would be one hell of a torch to take that heat.
92 Toyota pickup, 5VZFE, SAS, 30 splines, football cover, spooled and welded, 4.10s, SOS prototype rear disc brake conversion, soon to be Maryland inspected
Thought of prying the front legs apart? They look long enough to allow the deflection needed. And if done right you would bend the legs and not stess the joints. Course, changes to the railing may need to be made. Does the rear need to be lengthened a foot? If so, a sleeve joint could be fabricated and the one foot extension could be bolted instead of welded.
92 Toyota pickup, 5VZFE, SAS, 30 splines, football cover, spooled and welded, 4.10s, SOS prototype rear disc brake conversion, soon to be Maryland inspected
- Arya Ebrahimi
- Posts: 1896
- Joined: Tue Dec 14, 2004 10:58 pm
Yeah, the shop looked at doing that and of the four guys scratching their heads over what I wanted them to do, 2 of them said lets pry the front apart and 2 of them said either a funny bracket and/or some cutting and welding was the only way. As for the bow railing, it's coming off completely because a) I think it's going to get in the way and b) I think it looks better without a bow rail anyway. One shop I took it to has done work for me, my neighbor and my uncle ranging from fixing small shit up to rebuilding some farm implements and have always done a good job, they just don't often deal with structures like that tower which is where I think the money is coming into their quote. I want to take it to a T-top/tower builder, but this summer all the ones I called were up to their eyes in work already since it was boating season and they wanted nothing to do with it...I'm thinking winter may be the time to try and deal with someplace like that.MILLER wrote:Thought of prying the front legs apart? They look long enough to allow the deflection needed. And if done right you would bend the legs and not stess the joints. Course, changes to the railing may need to be made. Does the rear need to be lengthened a foot? If so, a sleeve joint could be fabricated and the one foot extension could be bolted instead of welded.
It sure is and I'd really appreciate any recommendations on where to go or how to do it.Arya Ebrahimi wrote: Where is the boat? If it's somewhere near Virginia Beach, I can call a few buddies and get a recommendation for a shop that might give you a more reasonable quote.
Thank y'all...who'd of thought that a 4wd club based 5 hours from the ocean could help me figure out a tower for an offshore fishing boat

Well, with Tech being an engineering school, there's a lot of know it alls, and I have a boat on the Potomac, so I am a know-it-all with some experience.
92 Toyota pickup, 5VZFE, SAS, 30 splines, football cover, spooled and welded, 4.10s, SOS prototype rear disc brake conversion, soon to be Maryland inspected
- Arya Ebrahimi
- Posts: 1896
- Joined: Tue Dec 14, 2004 10:58 pm
Ok, that wasn't as helpful as I thought it might be.
He suggested calling Mike's Marine. They're in Virginia Beach right off of Shore Drive. They don't actually build towers, but they do the canvas for lots of them, so they will probably have a good recommendation.
Tell them Jason Janezeck sent you(my buddy's name).
Ary
He suggested calling Mike's Marine. They're in Virginia Beach right off of Shore Drive. They don't actually build towers, but they do the canvas for lots of them, so they will probably have a good recommendation.
Tell them Jason Janezeck sent you(my buddy's name).
Ary